How Historical Data Reduces Fleet Costs
Explore how historical data and AI can significantly reduce fleet costs by optimising routes, cutting fuel consumption, and improving compliance.
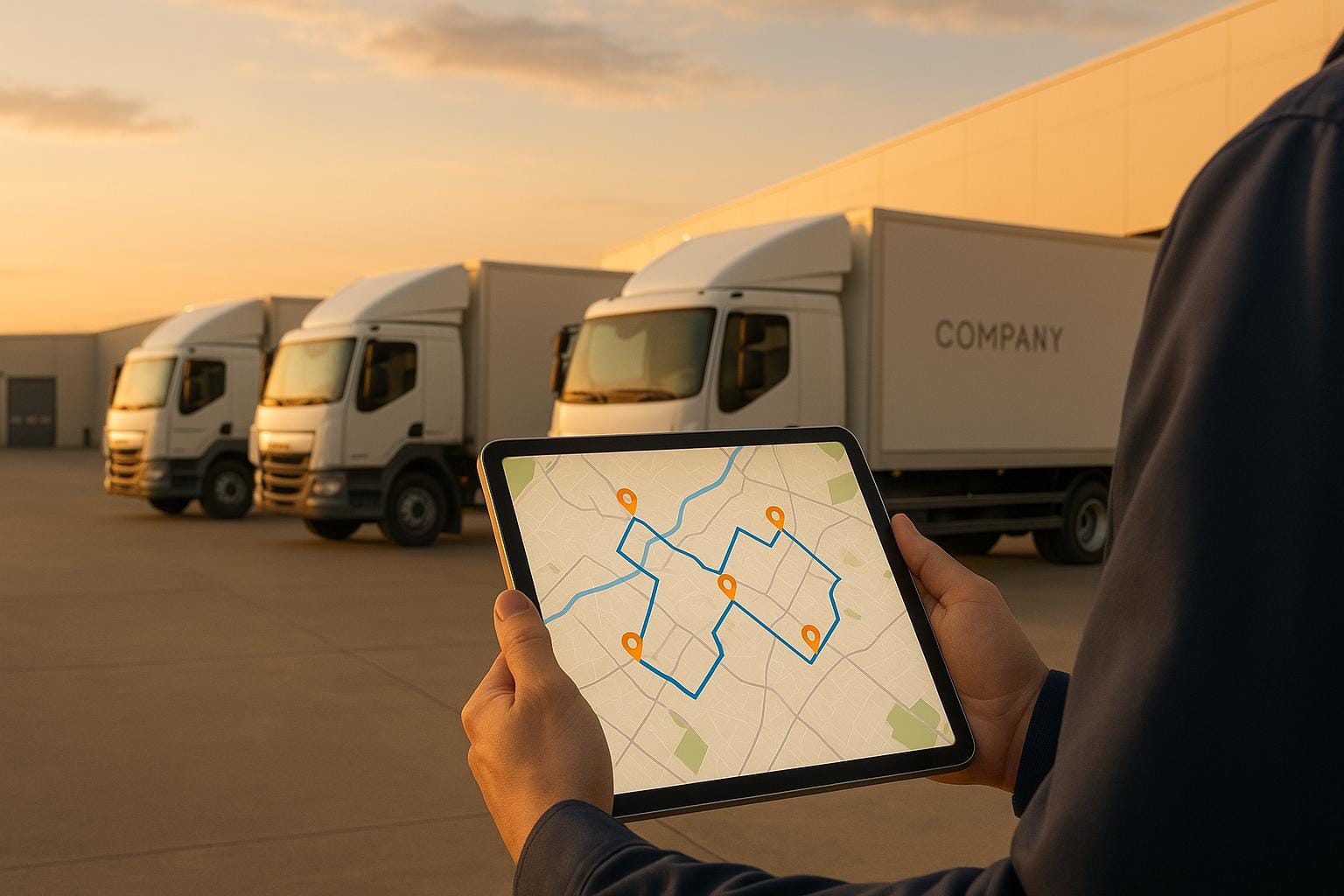
Fleet costs are rising, with fuel alone consuming up to 60% of budgets. Historical data offers UK businesses a clear way to cut these expenses. By analysing past journeys, traffic patterns, and driver behaviour, fleet managers can:
- Save up to 24% on fuel by identifying efficient routes and reducing unnecessary mileage.
- Lower overtime costs by planning realistic schedules based on previous data.
- Reduce maintenance expenses by predicting and preventing breakdowns.
- Improve compliance, avoiding fines in Clean Air Zones like London and Birmingham.
Telematics systems make this possible by combining historical insights with live traffic updates. Businesses using these tools report measurable savings in fuel, labour, and maintenance costs, while enhancing delivery reliability.
Data Intelligence for Long-Term Strategic Fleet Planning
How Historical Data Improves Route Planning
Historical data takes the guesswork out of route planning, turning it into a more precise and efficient process. By analysing patterns from previous journeys, fleet managers can make informed decisions that directly improve operational efficiency and cut costs. This data-driven strategy is transforming how UK businesses manage their fleets, building on earlier cost-saving measures to further streamline operations.
What Historical Data Brings to Fleet Management
Historical data offers a treasure trove of insights, including travel times, fuel consumption, and delivery efficiency. It also sheds light on traffic patterns, delivery schedules, and driver habits, helping fleet managers identify which routes are cost-effective and which are not. By studying these trends, managers can fine-tune future routes, reducing inefficiencies and improving overall performance. This method directly tackles the operational challenges discussed earlier.
AI and Historical Data: A Powerful Combination
Artificial intelligence takes historical data to the next level by combining it with real-time inputs like traffic updates, weather conditions, and customer preferences. AI systems continuously learn from past decisions, refining future route planning to achieve even better results. By using AI-powered algorithms, companies can cut delivery costs by up to 40% and reduce fuel expenses by as much as 30% by eliminating unnecessary mileage. Businesses that have implemented these systems often report substantial savings in both delivery and fuel costs.
Leveraging Vehicle Data for Compliance and Cost Savings
Historical vehicle data doesn’t just optimise routes - it also ensures compliance with UK traffic laws. When paired with AI, this data can predict traffic flows and help operators meet regulatory standards. For instance, AI considers factors like vehicle size, weight restrictions, and road limitations to assign the most suitable routes. Vehicle tracking systems further enhance compliance by monitoring driver behaviour and maintenance schedules, ensuring vehicles remain roadworthy.
Additionally, historical data aids in avoiding areas with strict emissions rules, such as London’s and Birmingham’s Clean Air Zones, helping businesses avoid hefty fines. Efficient route planning can also cut mileage by 20–30%, while predictive analytics have been linked to a 25% improvement in on-time deliveries. These enhancements not only save fuel and reduce overtime costs but also minimise regulatory penalties, creating a win-win for fleet operators.
How Historical Data Cuts Fleet Costs
The financial perks of using historical data become especially clear when you break down specific cost areas. Across the UK, fleet managers are leveraging data insights to make choices that translate directly into savings. These aren’t just theoretical gains - they’re real reductions in operating costs that can be measured in pounds.
Lower Fuel Bills and Fewer Miles Driven
Fuel is one of the biggest expenses for any fleet, which is why analysing historical data can be a game-changer. By studying past journeys, fleet managers can identify routes that drain more fuel than necessary and make adjustments to save money.
For instance, data reveals that erratic speed changes - like fluctuating between 75 and 85 km/h every 18 seconds - or driving at 120 km/h instead of 100 km/h can increase fuel consumption by as much as 20%. The sweet spot for efficiency lies between 50 and 80 km/h.
Telematics data also helps pinpoint inefficiencies like unnecessary idling and inefficient routes. Combined with GPS, this data enables real-time monitoring of traffic, road conditions, and weather, helping managers make immediate adjustments to routes and reduce idling in congested areas. Reviewing historical fleet card and telematics data can also highlight better routes, cutting down on miles driven and wasted fuel.
The benefits don’t stop at fuel savings. Optimising routes also leads to more predictable schedules, which can reduce delays and cut down on overtime.
Less Overtime and Lower Staff Costs
Route optimisation doesn’t just save on fuel - it also makes work schedules more efficient. Historical data provides accurate insights into how long routes and tasks actually take, helping managers avoid unnecessary overtime and reduce staffing costs.
For example, historical vehicle operation data can be used to automatically generate electronic timesheets. This eliminates the errors and guesswork of manual timesheets, cutting down on overtime expenses.
One UK fleet managed to cut its motor pool by 30% and save approximately £360,000 by using telematics data to refine their scheduling and billing processes.
Additionally, analysing past route completion times allows dispatchers to assign realistic schedules, avoiding delays that lead to overtime payments. By reducing time spent on the road through smarter route planning, fleets naturally lower overtime requirements.
Setting Up Historical Data Systems
Setting up a telematics system with a clear and structured approach - from selecting the right technology to training your staff - can provide historical data that reshapes how your fleet operates.
How to Add Fleet Telematics to Your Business
Start by outlining specific goals for tracking, such as reducing fuel costs, improving driver safety, or meeting regulatory requirements. These goals will guide you in identifying the features your system needs, like geofencing, driver behaviour monitoring, or detailed reporting capabilities.
Select technology that includes these features and integrates smoothly with your current fleet management software. This ensures a cohesive system that works seamlessly with your existing operations.
Make sure your telematics setup complies with UK laws, including the Road Traffic Act 1988, the Health and Safety at Work Act 1974, and the Data Protection Act 2018. Your telematics provider should also help you meet regulations like tachograph rules, the Working Time Directive, and environmental reporting standards.
Once the system is in place, train your team on how to use it effectively. Highlight its benefits, establish clear data usage policies, and set up a regular reporting routine.
From the start, focus on strong data management practices. This includes creating clear retention policies and performing regular audits. Additionally, ensure your telematics provider offers robust cybersecurity measures and full GDPR compliance. A well-managed system not only keeps data secure but also saves money by reducing inefficiencies.
Finally, integrate live data with your historical data to improve route planning and overall fleet efficiency.
Smart Routing: Using Past Data with Current Traffic
Once your telematics system is operational, you can combine historical data with live traffic updates for dynamic routing adjustments.
The real power of historical data lies in pairing it with real-time traffic insights. This combination allows your fleet to adapt quickly to changing conditions. Historical traffic data - sourced from navigation systems and mobile phone networks - forms a detailed database that route optimisation systems use to predict travel times and find the most efficient routes.
Dynamic rerouting becomes possible when these historical patterns are combined with real-time updates. This enables the system to redirect vehicles around accidents, construction zones, or unexpected congestion. The result? Fewer delays and lower costs from missed deliveries or overtime.
With GPS devices or mobile apps providing live updates, you can also analyse historical trends to predict peak traffic times and spot recurring bottlenecks. Route optimisation algorithms take into account factors like traffic conditions, road closures, weather, and delivery time windows. This allows you to plan deliveries during quieter periods and avoid problem areas. The outcome is fewer delays and reduced fuel and labour expenses.
GRS Fleet Telematics: Advanced Solutions for UK Businesses
Building on these strategies, GRS Fleet Telematics offers advanced solutions that combine historical and live data for smarter route planning.
GRS Fleet Telematics provides three hardware options for secure and continuous data collection:
- Essential Tracker (£35): A budget-friendly option for real-time tracking.
- Enhanced Option (£79): Adds a secondary Bluetooth backup for better theft protection.
- Ultimate Package (£99): Combines both trackers with immobilisation features for maximum security.
With dual-tracker technology, GRS Fleet Telematics ensures uninterrupted data collection and boasts a 91% recovery rate for stolen vehicles. The system is scalable, and the software subscription costs just £7.99 per vehicle per month, making it easy to expand data collection as your fleet grows without significant cost increases.
The platform simplifies the integration of historical and real-time data, so you don’t need IT expertise to benefit from advanced route optimisation. Installation is included when paired with fleet branding services, and the pay-per-recovery model means there are no upfront recovery fees.
As your business grows, ensure your telematics platform can handle increasing data demands, support new vehicle types like EVs, and accommodate additional users. GRS Fleet Telematics is built to scale, ensuring your historical data systems evolve alongside your operations.
Tracking Results and Making Improvements
Once your historical data system is up and running, it’s time to measure how well it’s working. Regular tracking not only helps you spot areas that need attention but also ensures your fleet is running as efficiently as possible, improving your return on investment (ROI).
Key Metrics to Monitor
After implementing route optimisation, the next step is keeping an eye on the numbers that matter most. These metrics give you a clear picture of your fleet’s performance and how it impacts your costs:
- Fuel efficiency: Fuel accounts for about 24% of a trucking fleet’s operational costs. Track fuel consumption (litres per 100 kilometres) for each vehicle, comparing performance by route and driver. This can help you spot trends and identify vehicles or drivers using more fuel than expected.
- Cost per delivery: This metric gives you a broad view of your operational efficiency. Calculate it by dividing your total operating costs by the number of deliveries completed. Include everything - fuel, labour, maintenance, and depreciation - and track it monthly to see how route optimisation affects profitability.
- Route adherence: Measure how closely drivers stick to planned routes. A good telematics system can flag deviations from optimal paths and time spent on unauthorised stops, which can point to areas for improving driver training or adjusting route plans.
- Driver behaviour: Metrics like speeding, harsh braking, and excessive idling impact both fuel usage and vehicle wear. Analysing this data helps you identify specific training needs for individual drivers.
- Vehicle recovery rates: For fleets with a focus on security, tracking recovery rates can help lower insurance costs and improve overall risk management.
Research shows that fleets using telematics systems often see a 10% to 15% drop in fuel consumption. Comparing your fleet’s performance against these industry benchmarks can help you evaluate how effective your system is.
Adjusting Strategies Based on Data
The data you collect isn’t just for tracking - it’s a tool for making better decisions. Regularly reviewing your historical data can uncover insights that might not be obvious in day-to-day operations. Use it to refine your strategies and keep costs in check.
- Monthly route analysis: Compare planned routes with actual trips logged by your telematics system. Look for consistent deviations - these might point to better routes or recurring traffic issues. Brian Antonellis, SVP at Fleet Advantage, highlights the importance of knowing “where you’re running and your valuable miles versus invaluable miles”.
- Seasonal trends: Historical data can help you prepare for predictable changes, like increased traffic or higher demand during certain times of the year. Use this information to adjust staffing and route planning.
- Driver coaching: Tailor training programmes to address specific issues, such as speeding or excessive idling. Focusing on individual drivers’ weaknesses makes training more effective and targeted.
- Preventive maintenance: Use data to spot patterns in breakdowns. If certain components fail more often, adjust your maintenance schedule to address these issues before they become costly emergencies.
- Delivery performance: Analyse delivery times to find routes that frequently run late. This can help you set more realistic delivery windows, improving customer satisfaction.
Advanced logistics analytics can cut transportation costs by up to 15%, while route optimisation often reduces fuel consumption by 5% to 10%. Regularly reviewing your data ensures these benefits are consistently realised.
Strategic use of technology based on historical data can also help you make the case for upgrades or new features by showing clear, measurable returns. Benchmarking against industry standards highlights where your fleet is excelling and where there’s room to improve, guiding your investment decisions.
Finally, consider this: 98% of car accidents are caused by human error. Analysing driver behaviour can reveal risky patterns, helping you address them before accidents occur. This proactive approach can save thousands of pounds in insurance claims and repair costs.
Review these metrics every quarter to ensure your system keeps delivering value. By setting clear improvement goals and tracking your progress, you’ll turn your data into actionable, cost-saving strategies.
Conclusion: Save More Money with Historical Data
Using historical data transforms fleet management into a smarter, cost-efficient operation by helping businesses make well-informed decisions. By examining past vehicle usage and route details, companies can spot patterns and adjust strategies to cut fuel consumption, manage overtime, fine-tune maintenance schedules, and enhance delivery performance.
Every journey and route provides opportunities to refine operations - whether it’s saving on fuel, reducing overtime, or planning maintenance more effectively. What makes historical data so powerful is its ability to fuel a cycle of continuous improvement. Over time, as more data is collected, predictions for maintenance become sharper, route planning gets smarter, and driver training becomes more focused, all contributing to long-term efficiency.
Thanks to specialised tools, these advantages are now within reach. Modern telematics systems offer an affordable way to harness data for fleet management. For example, GRS Fleet Telematics provides a solution starting at just £7.99 per month per vehicle. This platform combines real-time tracking with extensive data on vehicle performance. Features like geofencing and route efficiency monitoring allow businesses to implement cost-saving strategies effectively, while a 91% recovery rate adds an extra layer of financial security.
With these tools, businesses can achieve ongoing cost savings and operational excellence.
FAQs
How can businesses ensure their telematics systems meet UK legal and regulatory requirements?
To meet UK legal requirements, businesses must secure clear and informed consent from drivers, clearly outlining how telematics data will be gathered and used. This process must align with GDPR and the Data Protection Act, ensuring employee privacy is respected and transparency is upheld throughout.
Telematics systems should also be configured to aid compliance. For instance, they can include features like linking driver identification to valid licences and implementing strong data security protocols. Regularly updating policies and adhering to official guidelines not only helps maintain legal compliance but also builds trust with employees.
How can I set up a telematics system to use historical data for reducing fleet costs?
Setting up a telematics system to make the most of historical data involves a few essential steps:
- Install the telematics device: Connect the device to the vehicle’s OBD-II port or another suitable interface. Make sure it’s securely in place and working as it should.
- Set up data collection: Configure the system to capture key information like GPS locations, engine performance, and driver behaviour. This data serves as the backbone for any meaningful analysis.
- Dive into historical data: Use analysis tools to uncover trends and patterns. This can help refine routes, cut down on delays, and boost overall efficiency.
By taking these steps, businesses can turn historical data into actionable insights, helping to lower fleet costs and improve productivity.
How does using historical data, AI, and real-time inputs improve route planning and reduce fleet costs?
By blending historical data with AI and real-time information, businesses can craft smarter, more efficient route plans that help reduce operational costs. AI examines past journey records alongside live traffic updates, weather conditions, and other variables to predict and adjust routes on the fly. The result? Lower fuel consumption, fewer delays, and faster delivery times.
On top of that, AI-driven predictive analytics can spot potential vehicle issues early, cutting down on unexpected downtime and reducing maintenance costs. These technologies work hand in hand to streamline fleet performance and deliver noticeable savings for businesses.