8 Best Practices for Fleet Maintenance Scheduling
Learn best practices for fleet maintenance scheduling to enhance vehicle safety, reduce costs, and prolong fleet lifespan.
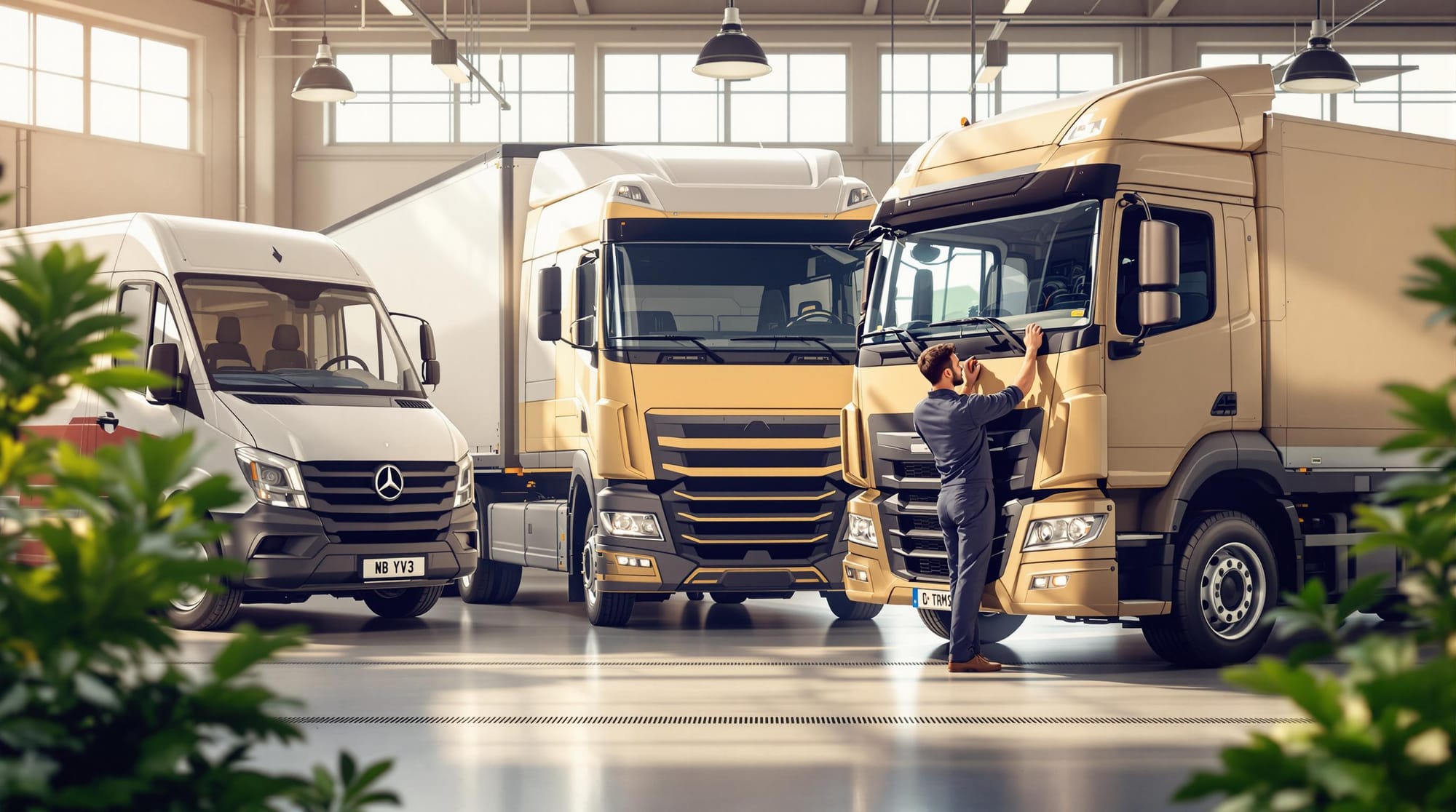
Maintaining your fleet properly can save money, reduce downtime, and improve vehicle safety. Poor maintenance costs can reach £760 per vehicle daily, and a single crash might cost over £20,000. Here’s how to stay ahead:
- Set Regular Maintenance Plans: Include preventive, predictive, and corrective maintenance tailored to vehicle usage.
- Use Telematics Data: Monitor real-time vehicle health, automate alerts, and track diagnostics to prevent costly repairs.
- Centralise Records: Keep all service history, costs, and inspection reports in one digital system.
- Automate Alerts: Set reminders for servicing based on mileage, time, or diagnostics.
- Incorporate Driver Feedback: Train drivers to report issues early for faster fixes.
- Go Digital: Use cloud-based tools for tracking costs, diagnostics, and maintenance schedules.
- Match Schedules to Vehicles: Adjust maintenance frequency based on vehicle type, age, and usage.
- Train Staff: Ensure your team knows how to use new systems effectively.
Quick Comparison
Practice | Key Benefit |
---|---|
Regular Maintenance Plans | Extends vehicle lifespan |
Telematics Data | Reduces breakdowns |
Centralised Records | Simplifies audits |
Automated Alerts | Prevents missed servicing |
Driver Feedback | Catches issues early |
Digital Tracking | Cuts costs and minimises downtime |
Vehicle-Based Schedules | Customised care for each vehicle |
Staff Training | Maximises system effectiveness |
How to choose the right fleet maintenance software - Part 1
1. Set Up Regular Maintenance Plans
Keep your fleet running smoothly and extend its lifespan with a well-organised maintenance plan. This approach ensures your vehicles stay dependable and efficient.
A solid maintenance plan should include three main types:
- Preventive Maintenance: Regularly inspect oil and filters, brakes, tyre pressure and wear, battery performance, and fluid levels.
- Predictive Maintenance: Use telematics to monitor engine performance, fuel consumption, component wear, and overall vehicle usage.
- Corrective Maintenance: Quickly address unexpected problems as they occur and maintain detailed repair records for future reference.
Customise service intervals based on each vehicle's usage, operating conditions, and historical performance data. This tailored strategy helps you schedule checks, major services, and inspections at the right times, ensuring your fleet stays in top condition.
2. Use Telematics Data for Maintenance Timing
Telematics systems make it easier to schedule maintenance by providing real-time insights into vehicle health. These systems gather key data directly from your vehicles' engine control modules (ECM).
Automated Odometer Tracking
By connecting telematics devices to fleet management software, you can automatically track daily mileage. This ensures that maintenance schedules are based on actual vehicle use. You can also set up automated notifications to remind you when servicing is due, using precise odometer readings.
Real-time Diagnostic Monitoring
Telematics systems send instant alerts for diagnostic trouble codes (DTCs), allowing you to tackle issues early before they become costly repairs. They can even generate digital work orders automatically to streamline repair efforts. Keeping an eye on these diagnostics helps prevent small problems from turning into major headaches.
"With GPS tracking and on-board diagnostic reading capabilities, telematics collects data directly from an asset to provide detailed information around asset usage, driver behaviour, fuel consumption and diagnostic trouble codes (DTCs)." - Rachael Plant, Senior Content Marketing Specialist, Fleetio
Key Performance Metrics to Monitor
Metric | Why It Matters for Maintenance |
---|---|
Fuel Consumption | Spikes might signal engine inefficiency |
Driver Behaviour | Harsh driving can cause faster wear and tear |
Odometer Readings | Accurate mileage ensures timely servicing |
Diagnostic Trouble Codes | Early warnings help avoid major repairs |
These metrics help fine-tune your maintenance plans and reduce unexpected downtime.
Streamlined Maintenance Workflow
Integrating telematics data with cloud-based systems lets you:
- Monitor vehicle health as it happens
- Automate maintenance schedules based on actual usage
- Keep a detailed repair history to spot recurring problems
- Reduce downtime with proactive servicing
This data-driven approach ensures your fleet runs smoothly and efficiently.
3. Keep All Maintenance Records in One Place
Organise all maintenance records in a single location to simplify fleet management and cut costs. This method makes accessing records easier and improves decision-making, building on telematics-driven maintenance strategies.
Digital Record Management
Switching to cloud-based tools simplifies how records are kept, creating a digital profile for every vehicle.
Record Type | Why It Matters |
---|---|
Service History | Tracks all repairs and maintenance per vehicle |
Cost Records | Monitors expenses and identifies cost patterns |
Inspection Reports | Ensures compliance and safety documentation |
Vehicle Profiles | Provides quick access to specific vehicle data |
Smarter Decisions
Having all records in one place helps fleet managers schedule maintenance more accurately and use resources more effectively. It also makes it easier to spot recurring problems, track individual vehicle costs, monitor service intervals, and plan preventive maintenance.
"Getting company records in order is a small investment on the scale of an operations and maintenance (O&M) program, but it produces massive dividends in the form of an optimised system that delivers better results." – IMPO
Access on the Go
With mobile features, you can update records in real time, upload photos of defects, check vehicle history on-site, and submit digital inspection reports.
Stay Compliant
Centralised records make audits easier and help you stay compliant with regulations.
Track Performance
Consolidated data provides clear insights into fleet efficiency and trends, helping you refine operations and plan for the future.
4. Set Up Automatic Service Alerts
Automated service alerts help you avoid expensive mistakes and keep your fleet running smoothly. With real-time data from telematics devices, you can build a maintenance system that notifies you about upcoming service needs.
Notifications Across Multiple Channels
Set up alerts across different platforms to ensure you never miss a service reminder:
- Email: Get detailed service requirements straight to your inbox.
- Web Dashboard: Monitor alerts from a centralised platform.
- Mobile Push Notifications: Stay updated with critical alerts on the go.
Staggered Alert System
Implement a staggered alert schedule to give you enough time to prepare:
Alert Stage | Timing | Purpose |
---|---|---|
Initial Warning | 7 days or 1,000 miles beforehand | Allows for scheduling |
Final Reminder | 3 days or 200 miles beforehand | Signals urgent action |
Key Tracking Metrics
Telematics systems rely on essential data to trigger alerts, including:
- Odometer readings
- Engine hours
- MOT deadlines
- Regular service intervals
Tailored Alert Settings
Customise alerts to match the specific needs of each vehicle and your fleet's operations. This ensures every vehicle gets the right attention without overwhelming your staff with unnecessary notifications. It’s a practical way to enhance your maintenance strategy.
Centralised Dashboard
A single dashboard lets you easily track:
- Vehicles due for service
- Scheduled maintenance tasks
- Completed service records
- Service history trends
5. Include Driver Reports in Planning
Driver feedback acts as an early-warning system. Those behind the wheel every day often notice issues before they become serious.
Daily Vehicle Checks
Set up a clear process for drivers to record their observations. Pre-shift and post-shift inspections should include checks for unusual sounds, vibrations, or performance changes. Catching these early can help avoid expensive repairs.
Common Warning Signs
Teach drivers to spot and report these critical warning signs:
Warning Sign | What to Check | Priority Level |
---|---|---|
Unusual Engine Noise | Engine performance, oil levels | High |
Steering Vibrations | Wheel alignment, tyre condition | Medium |
Delayed Braking | Brake pad wear, fluid levels | High |
Dashboard Warning Lights | Specific system indicated | Immediate |
Exhaust Changes | Emissions system, engine health | Medium |
Standardised Reporting Process
Having a consistent reporting process ensures no important details are missed. This system makes it easier to train drivers and connect their feedback with your maintenance plans.
Driver Training Benefits
Incorporating driver insights into your maintenance routine can:
- Spot safety issues before they escalate
- Reduce the chances of unexpected breakdowns
- Improve the accuracy of maintenance schedules
- Avoid major mechanical failures
"Make sure your drivers understand the importance of proper vehicle maintenance. Encourage them to report any issues they notice during their shifts." - SafetyCulture
Integration with Maintenance Systems
Combining driver reports with telematics data creates a more responsive maintenance plan. When drivers flag issues, the maintenance team can quickly evaluate the problem and adjust service schedules. This approach helps tackle minor problems early, avoiding larger, costlier repairs and keeping vehicles on the road.
6. Use Digital Maintenance Tracking
Digital maintenance tracking goes beyond basic alerts and record-keeping by offering real-time insights and automating cost control. These systems simplify fleet maintenance, reduce manual effort, and improve efficiency by utilising real-time data and cloud connectivity.
Better Monitoring with Digital Systems
Digital tracking systems give you instant access to essential information:
Monitoring Area | Benefits | Impact on Operations |
---|---|---|
Engine Diagnostics | Detects faults early | Minimises unexpected breakdowns |
Component Health | Tracks oil life, battery, and brakes | Prevents component failures |
Service History | Maintains complete records | Ensures compliance and warranty protection |
Cost Tracking | Monitors expenses in detail | Helps manage maintenance budgets |
Automated Maintenance Alerts
These systems send automatic reminders when services are due. This proactive approach can significantly reduce issues - studies show automated maintenance tracking helps prevent up to 60% of roadside inspection violations.
Lower Operating Costs
Digital tracking systems help cut expenses by:
- Reducing downtime costs (estimated at £350–£600 per vehicle daily)
- Detecting problems early to avoid costly repairs
- Ensuring warranty compliance
- Simplifying parts management
"The automation that comes with electronic vehicle inspection and maintenance solutions can prove invaluable in reducing your fleet's manual effort and improving operational effectiveness."
– Tom Bray, Sr. Industry Business Advisor, J. J. Keller & Associates, Inc.
Cloud-Based Accessibility
With cloud-based systems, maintenance data is stored securely and offers several key benefits:
- Secure Storage: Keeps documentation safe and backed up
- Universal Access: View records from anywhere
- Real-Time Updates: Instantly reflects system-wide changes
- Simplified Reporting: Generates detailed reports quickly
Integration with Telematics
These systems also integrate seamlessly with telematics, refining maintenance schedules further. By using telematics data, they can predict maintenance needs based on actual vehicle usage, ensuring services are performed before issues arise.
A March 2024 survey by Limble highlighted downtime as the top challenge for maintenance teams, showing how critical digital tracking systems are for modern fleet management. Implementing a Computerised Maintenance Management System (CMMS) enables fleets to automate schedules, streamline vehicle inspections, and manage parts purchases efficiently.
7. Match Schedules to Vehicle Types
Aligning maintenance schedules with vehicle types helps improve efficiency and reduce downtime. This approach works well alongside the digital tracking methods discussed earlier.
Vehicle Categories and Maintenance Needs
Different vehicles have specific maintenance requirements based on their roles:
Vehicle Type | Maintenance Frequency | Key Focus Areas |
---|---|---|
Light-duty Vans | Every 7,500 miles or 6 months | Oil changes, brake inspections, tyre rotation |
Heavy-duty Lorries | Every 12,500 miles or 3 months | Engine diagnostics, transmission checks, air systems |
Specialised Equipment | Based on operating hours | Hydraulic systems, safety equipment, auxiliary components |
Usage-Based Adjustments
Tailor maintenance intervals by considering:
- Driving conditions (e.g., urban roads vs. motorways)
- Load requirements
- Daily mileage
Age-Related Adjustments
For vehicles over five years old, increase inspection frequency. Pay extra attention to wear-prone parts and perform detailed fluid analysis. These adjustments help create a more tailored plan for older vehicles.
Steps for Customising Maintenance
-
Fleet Assessment
Begin by categorising your fleet based on vehicle type, usage patterns, and operational priorities. This information forms the foundation for tailored schedules. -
Baseline Requirements
Review manufacturer guidelines and industry norms for maintenance intervals. Use historical performance data to refine these benchmarks. -
Monitor and Adjust
Continuously evaluate vehicle performance data to fine-tune schedules and ensure optimal maintenance timing.
Integration with Digital Systems
Leverage telematics to update schedules in real time. This prevents unnecessary servicing while avoiding delays that could lead to breakdowns.
8. Keep Staff Updated on New Systems
Introducing digital tracking systems in fleet maintenance requires thorough staff training to make the most of these tools. Once implemented, ensuring your team has the right skills is key to achieving the best outcomes.
Training Programme Overview
Training Area | Key Topics | Timeline |
---|---|---|
System Navigation | Using the interface, entering data | Week 1-2 |
Data Analysis | Identifying trends, planning ahead | Week 3-4 |
Emergency Protocols | Troubleshooting, backup procedures | Week 5 |
Advanced Features | Custom reports, integration options | Week 6-8 |
Key Training Steps
Start by evaluating your team's current skills. Then, provide hands-on practice in areas like managing records, creating reports, and setting up alerts. Focus on helping staff become proficient in:
- Managing maintenance records
- Generating service reports
- Configuring alerts
- Analysing performance data
Ongoing Support
Offer regular refresher courses, keep training materials up to date with system updates, and encourage team members to share their knowledge. This approach helps embed the new systems into daily workflows smoothly.
Useful Resources
Equip your team with easy-to-follow resources, such as:
- Step-by-step guides
- Troubleshooting manuals
- Quick-reference cards
- Video tutorials
Evaluating Training Effectiveness
Monitor how well the training is working by measuring:
- Staff confidence in using the system
- Reduction in errors
- Improved task completion times
- Accuracy of records
Ensuring a Smooth Rollout
Support the transition by:
- Offering dedicated help during the rollout phase
- Establishing clear communication channels
- Collecting feedback for continuous improvement
When staff are well-trained in these digital tools, they directly enhance the fleet's maintenance strategy, boosting vehicle reliability and minimising downtime.
Maintenance Types and Tracking
Understand the difference between scheduled and data-driven maintenance to improve fleet efficiency.
Comparing Maintenance Approaches
Aspect | Scheduled Maintenance | Data-Driven Maintenance |
---|---|---|
Timing Basis | Fixed intervals based on mileage or time | Alerts triggered by real-time vehicle data |
Cost Efficiency | Can lead to over- or under-maintenance | Matches the actual condition of the vehicle |
Resource Planning | Predictable scheduling | More adaptable |
Vehicle Availability | May cause unnecessary downtime | Aims to maximise operational time |
These differences highlight the importance of tracking the right metrics for a proactive maintenance plan.
Key Tracking Metrics
To optimise maintenance, focus on metrics like:
- Engine hours and mileage readings
- Fault code alerts
- Results from fluid sample analyses
- Fuel consumption trends
Benefits of Data-Driven Maintenance
By tailoring maintenance to a vehicle's actual condition, you can minimise unplanned downtime and control costs more effectively.
Steps for Implementation
-
Data Collection Systems
Install telematics to gather essential vehicle data. -
Analysis Tools
Use software to interpret and make sense of the collected data. -
Integration Strategy
Connect tracking systems with scheduling tools for a streamlined process.
Once implemented, regularly evaluate the system's performance to ensure it meets your goals.
Performance Monitoring
Assess the results of your maintenance strategy by tracking:
- Vehicle downtime
- Cost per kilometre
- Frequency of emergency repairs
- Overall fleet reliability
Conclusion
Planning fleet maintenance effectively can save money and improve vehicle reliability. These potential savings highlight the importance of staying ahead with maintenance schedules.
Using tools like GRS Fleet Telematics allows fleet managers to monitor key metrics such as engine hours and fuel usage, ensuring maintenance is carried out on time. Predictive maintenance has changed the game, offering a smarter way to handle vehicle care.
"By implementing predictive and preventative maintenance processes across their fleets, managers can help reduce downtime, prevent unexpected issues, and bring costs under control."
Proactive maintenance scheduling offers several practical benefits, including:
- Better fuel efficiency
- Longer vehicle lifespan
- Lower emergency repair expenses
- Enhanced safety and compliance
- Smarter use of resources
GRS Fleet Telematics supports this approach with real-time monitoring and automatic alerts. Starting at just £7.99 per vehicle per month, the platform provides everything needed to keep fleets running smoothly while cutting down on costs.